Induction heating
- Induction heating is based on the principle of Faradays law of mutual induction. Induction heating process makes use of currents induced by electromagnetic action in the material to be heated (ie transformer principle).
- There is a primary winding through which an AC current is passed. This coil is magnetically coupled with the metal to be heated. An electric current is induced in this metal when AC current is passed through the primary heating coil.
- The value of induced current depends on a) Magnitude of primary current b) The ratio of number of turns in the primary and secondary circuit c) The co-efficient of magnetic coupling.
- Induction heating is used for heating only conducting materials (Ferromagnetic and non-magnetic)
- Magnetic materials generally have high permeability and resistance than non magnetic material. Thus the Induction heating is more adoptable and economical for treating magnetic materials.
Induction furnaces are further classified as:
- Core type induction furnace
- Core less induction furnace.
Core type direct induction furnace:
The core type of furnace is essentially a transformer in which the charge forms the secondary circuit. Charge is placed in the annular hearth which forms the single turn secondary circuit of the transformer. The charge is magnetically coupled to the primary by an iron core as shown in figure. To start the furnace, molten metal is poured in the annular hearth, otherwise the secondary winding is incomplete (open) and no current will flow through the charge and no heating will take place. In this type furnace an iron ring is placed at the bottom of the hearth.
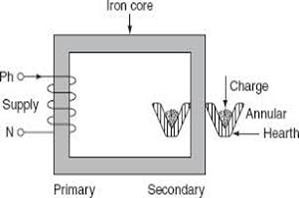
It can be seen from the diagram that the magnetic coupling between primary and secondary is very poor, resulting in high leakage current and a low power factor. Also the electromagnetic forces cause severe turbulence and stirring action if operated at normal frequency. Due to above two reasons, the furnace is operated at low frequencies of the order of 10 Hz. An additional motor generator set or frequency converter is needed to obtain this low frequency.
- In this type, current density of the charge is to be limited to about 480-500A per sq.m, above this current density will produce high electromagnetic force in the molten metal and it will cause adjascent molecules of the molten metal carrying the current in the same direction to repel each other because similar charges repel.The repelsion may cause interruption of the secondarycircuit. This effect is called as Pinch effect. It depends frequency. and it has low effect at lower frequency.
Disadvantages:
- A crucible of inconvenient shape is required.
- High leakage current & Low power factor due to poor magnetic coupling. To compensate this Furnace is operated at low frequencies of the order of 10 Hz.
- A Motor Generator set or frequency converter is required
- Some molten metal is necessary in the crucible to start the furnace
- It is bulky due to the presence of core
Recent Comments